Технология производства круп
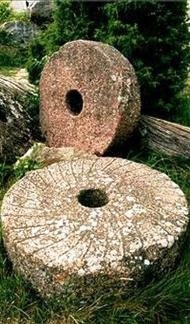
Задачей крупяного производства является переработка зерен различных культур в крупы и крупяные продукты. В настоящее время производится на сложном высокотехнологичном оборудовании, позволяющем получать продукцию высокого качества и унифицировать производство для разных видов сырья.
История возникновения крупяного производства
Необходимость в переработке зерна появилась непосредственно с расширением земледелия, то есть практически на заре зарождения цивилизации.
История развития машин для обработки зерна — классический пример развития машин и перехода используемых источников энергии от ручного привода, воды и ветряных мельниц к современным электродвигателям. Развитие таких компаний породило некоторые научные идеи. В частности, исследование роли трения в механизмах проводилось на примере работы шестерен водяной мельницы.
Примечательно, что в процессе эволюции менялись только источник энергии и материалы, из которых изготавливаются приспособления для очистки зерна. Важно, что процесс не изменился с древних времен. Это трение зерен об абразивную поверхность для очистки их от внешних оболочек.
Технологический процесс крупяного производства
Процесс создания крупы на производстве делится на этапы: подготовка зерна к переработке и получение готовой крупы. Основным показателем качества конечного продукта является содержание однородного ядра без остатков лущеного зерна и фракционированных частиц и пыли.
Первичная обработка зерна
Первый этап — механическая очистка зерна от примесей в виде металломагнитных фракций, минеральных включений, семян сорняков, нежидких семян. Основной процесс направлен на отделение нежелательных примесей от полезной массы. Это делается с помощью магнитных сепараторов, пылесосов, стоек, триеров, кусторезов.
Магнитные сепараторы предназначены для отделения металломагнитных элементов, которые могли случайно попасть в зерно при уборке или транспортировке. В общем случае это постоянный магнит, под которым проходит зерно. Магнит удаляет все нежелательные металлические включения.
Стоунеры предназначены для разделения зерна на две фракции по удельному весу. Разделение происходит с помощью подвижной платформы и регулируемого направления потока воздуха. При этом поступающий материал разделяется на чистый продукт и тяжелые примеси.
Триер сортирует по длине чистые семена и удаляет нежелательные длинные или короткие зерна других культур.
Поломоечная машина очищает зерна от пыли, грязи и фрагментарного отделения кожуры фруктов.
Промежуточный этап: гидротермическая обработка
Промежуточным этапом для некоторых культур, таких как овес и горох, является гидротермическая обработка. Смысл операции: пропаривание зерна под давлением в течение 3-5 минут. Пропаривание увеличивает прочность зерна и снижает впитываемость из-за клейстеризации крахмала во внешних частях эндосперма. Шелуха фасоли также становится тоньше, и с нее легче отделить семена. Повышаются вкусовые качества и уменьшается количество молотого продукта:
- В зерне овса кондиционирование удаляет горечь некоторых ферментов;
- Срок годности зерновых продуктов увеличивается;
- Время варки обработанной таким образом крупы сокращается.
Процесс темперирования проходит в три этапа: увлажнение и прогрев зерна паром с последующей сушкой и доведением зерна до стабильной температуры.
Конструкция охлаждающей колонны представляет собой набор штампованных сит, через которые зерно постепенно опускается, при этом подвергаясь интенсивному обдуву.
Шелушение сухого, но горячего зерна требует более интенсивных действий, что увеличивает количество перемалываемого зерна и снижает производительность. Поэтому после сушки необходимо охлаждать зерно охлаждающей колонной.
Структура зерна достаточно ломкая, поэтому при переработке возникает проблема образования большого количества дробленого зерна и муки. Для упрочнения активной зоны и проведения гидротермических обработок используют вертикальные и горизонтальные испарители, паровые сушилки и вертикальные охлаждающие колонны.
Готовая крупа сортируется по номерам, исходя из размера фракции конечного продукта. Например, кукурузная крупа оценивается пятью баллами, а ячменная крупа — тремя баллами.
Конечный этап крупяного производства
Зерна начинаются с процесса деления зерен по размеру. Ядра одного формата легче чистятся и меньше дробятся при обработке. Гречка, горох и овес разделены по размеру, а кукуруза, пшеница и ячмень разделены только мелкими зернами.
После этого зерно очищается в шелушильных и вальцовых машинах. Конечным продуктом этапа является цельное зерно. Получают также дробленое, рубленое и неочищенное зерно, шелуху (лузгу) и муку (мелкоизмельченные частицы зерна). Измельчение зерна заканчивается. Это делается для того, чтобы конечный продукт имел однородный цвет и практически одинаковую форму.
Рис и горох также полируют, чтобы получить гладкую поверхность. Полированные каши, по сравнению с необработанными, содержат больше крахмала, лучше усваиваются и быстрее готовятся.
Технологии для изготовления хлопьев
Для получения хлопьев быстрого приготовления зерно подвергают одной из следующих технологий:
- Гидротермальная обработка + плющение.
- Обработка зерна инфракрасными лучами.
- Обрабатывается в экструзионных камерах.
Микронизация – это процесс термической обработки зерна с помощью инфракрасных лучей. Под действием молнии внутриклеточная вода закипает, образуя внутри зерна избыточное давление, которое разрывает молекулы крахмала и набухает зерно.
Экструзия – это процесс, при котором крупа подвергается высокому давлению и температуре в камерах экструдера, а на выходе из-за большого перепада давления и температурного режима происходит мгновенное испарение воды и увеличение объема зерна.
Сушка чешуи в основном осуществляется с помощью аэровибрационных сушилок.
Проектирование комплекса крупяного производства
Основное направление проектирования – создание автоматизированных производственных комплексов с высоким уровнем компьютеризации, уменьшением количества ручного труда и контролем за производством и продукцией на всех стадиях переработки зерна.
В настоящее время распространенным техническим решением при проектировании крупяного производственного комплекса является расчет и проектирование «под ключ» всего производственного оборудования. С помощью этой опции можно адаптировать комплекс к конкретным условиям и требованиям, повысить эффективность и производительность.
Проблемы, которые следует учитывать при проектировании ККП
Влажность зерна является основным параметром перед поступлением на переработку, так как производительность всего технологического оборудования напрямую зависит от процентного содержания воды в общей массе перерабатываемого сырья. Поэтому часто применяют системы искусственной термообработки (сушилки).
Для контроля качества крупы необходимо проводить лабораторные исследования. Во-первых, такие параметры, как:
- Влажность;
- Наличие посторонних примесей;
- Качество зерна.
Также часто возникают проблемы с логистикой. Необходимость обеспечения максимально эффективной системы доставки сырья и отгрузки готовой продукции для обеспечения полной загрузки и бесперебойной работы комплекса. Чаще всего в целях минимизации транспортных расходов предприятия по производству зерна строят вблизи элеваторов и амбаров.
Для хранения готовой продукции на территории предприятия часто проектируют склад готовой продукции, рассчитанный не менее чем на 5 суток полной производительности завода. Бункер приема зерна при полном заполнении должен обеспечивать суточную потребность перерабатывающего предприятия в сырье.
Поэтому металл заменяют пластиком, который более безопасен в использовании!
Снижение пожароопасности на предприятиях по производству круп гарантируется применением полимерных материалов, препятствующих возникновению искр и локальному нагреву при ударах или трении поверхностей. Наиболее частым местом возникновения взрывов и первичных пожаров являются лифты. Причиной таких случаев являются металлические ковши, которые при ударе о трубу стояка могут образовывать искры, способные воспламенить пылевоздушную смесь.
Кроме того, износостойкость полимеров намного выше и позволяет увеличить срок службы деталей, контактирующих с зерном, а значит, уменьшить количество выделяемой пыли.
По сравнению с металлическими деталями полимерные детали имеют меньшую твердость и меньше повреждают обрабатываемое зерно.
Выяснилось, что при эксплуатации металлических труб, в которых транспортировка зерна осуществляется самотеком, в наиболее нагруженных линиях происходит быстрый износ стенок труб, в результате чего образуются сквозные отверстия. Пыль просачивается через них и увеличивает общую запыленность производственного цеха. Накапливаясь на стенах и оборудовании, пыль образует легковоспламеняющийся аэрозоль, который при искрообразовании может тлеть, а при образовании пылевого облака может вызвать взрыв.
Поэтому по возможности для транспортировки зерна используют полимерные трубы, которые меньше подвержены износу. Антипригарные свойства пластика препятствуют скоплению пыли и налипанию корпусов в труднодоступных местах на машинах и механизмах. Исключение появления локальных самоподогревов и зон обогрева.
Итог
Технология производства круп не стоит на месте. Постоянно увеличивается процент автоматизации производства, повышается производительность машин и механизмов за счет внедрения новейших конструкторских решений и использования новых материалов. Каждое инновационное решение увеличивает ассортимент различных каш с разными вкусовыми свойствами.