Технология изготовления древесноволокнистых плит ДВП
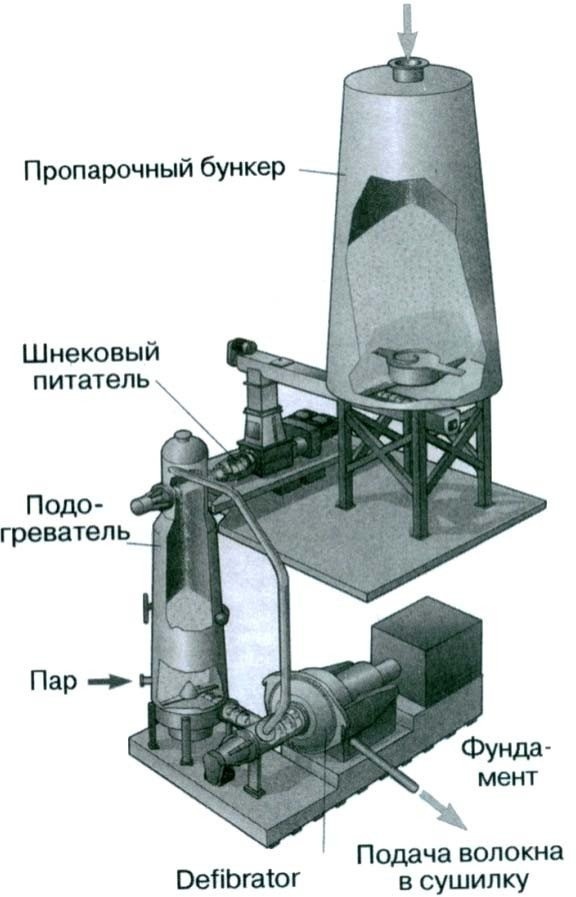
Производство древесноволокнистых плит основано на технологических процессах расщепления древесины на волокна, обеспечивающих прочное взаимодействие волокон друг с другом в процессе формирования плиты.
Сырьем для производства ДВП может быть как круглый лес, так и технологическая щепа, полученная из некачественной древесины, и древесные отходы лиственных и хвойных пород (ель, сосна, береза, осина, дуб, бук и др.). Сырьем, кроме древесины, могут служить лубяные растения с волокнистой структурой (тростник, тростник, стебли хлопчатника и др.); однако пока они не нашли применения в производстве плит в нашей стране.
Сырьем для изготовления плит МДФ служат в основном круглый лес и отходы лесопиления лиственных и хвойных пород. Из хвойной древесины получают качественные легкие доски.
В технологии производства плит в древесноволокнистую массу вводят связующее, гидрофобизаторы, осадители и другие добавки.
В качестве отвердителей (связующих) обычно используют фенолформальдегидные смолы, реже сосновую канифоль и органические изоцианаты (дифенилметандиизоцианат). Из фенолформальдегидных смол применяют смолы резольного типа, в основном марок СФЖ-3014 и СФЖ-3024Б. Канифоль иногда используется в качестве упрочняющей добавки при производстве мягких древесноволокнистых плит.
При намокании пластины не только деформируются, но и набухают и увеличиваются в размерах. Для придания ДВП определенной водостойкости и гидрофобности применяют водоотталкивающие вещества: парафин, церезин, церезиновый состав и дистиллированный шлак. Введение любого из этих веществ в небольшом количестве (до 1%) резко повышает водостойкость плит. Добавление большого количества веществ снижает прочность пластин и становится нецелесообразным.
В древесноволокнистую массу вводят водоотталкивающие добавки в виде специально приготовленных щелочных эмульсий, разбавленных горячей водой. Это достигается интенсивным перемешиванием с добавлением эмульгатора. В качестве эмульгатора используют олеиновую кислоту с аммиаком, лигносульфонат (дрожжевую сульфатную массу) и остатки синтетических жирных кислот.
Осадители представляют собой вещества, которые способствуют осаждению в водной суспензии проклеивающих композиций на древесных волокнах. Наиболее часто используемыми осадителями являются сульфат алюминия и серная кислота.
В производстве специальных древесноволокнистых плит, как мокрым, так и сухим способом, используются различные химические добавки. Например, для повышения водостойкости ДВП их пропитывают талловым маслом с влагопоглотителем, госсиполовой смолой, остатком низкомолекулярного полиэтилена и др. мягкие и полутвердые плиты пропитывают нефтяным битумом. Для получения огнеупорных плит при мокром способе производства в древесноволокнистую массу вводят антипирен нефелин с добавлением асбеста, а при сухом — фосфаты и сульфаты аммония, буру, борную кислоту и др.
1. Технология изготовления ДВП мокрым способом производства
Щепа, изготовленная в рубительной машине, обязательно сортируется на трехъярусных ситах: размер верхнего сита 39×39, нижнего 5×5 мм. Крупную фракцию измельчают в дезинтеграторах. Щепа без морщинистых краев, с длиной частиц 10-35 мм, толщиной не более 5 мм, с углом резания 30-60 градусов используется в производстве древесноволокнистых плит. Допускается содержание гнили не более 5 %, минеральных включений не более 1 %, коры не более 15 %.
Оптимальная влажность щепы перед измельчением составляет 50-70 %, при истирании снижается примерно на 30 %.
Основой производства качественных плит является высокое качество древесных волокон, однородность свойств и геометрических размеров. Первичный горячий помол щепы осуществляют в измельчителях, вторичный — в рафинерах или конусных мельницах. Внешний вид системы измельчения Дефибратор показан на рис. 1. Он состоит из испарительного бункера (камеры) со шнековым питателем, подогревателя, шнековой системы подачи и помольной установки. Паровой бункер предназначен для выравнивания температуры и влажности древесно-стружечной массы с повышением температуры до 80-90 0С. Воздействие пара на щепу делает ее менее хрупкой и сглаживает реакцию на динамические нагрузки.В зону помола могут подаваться добавки специального назначения: гидрофобизаторы, модификаторы и др.
Рис. 1. Система измельчения измельчителя
Степень измельчения теста измеряется в аппарате «Второй дефибратор», характеризуется степенями измельчения и имеет обозначение ДС. Для твердых плит степень полировки должна быть в пределах 22-28 ДК, для мягких 28-35 ДК.
На рис. На рис. 2 показано, чем отличаются волокна, выходящие из дефибратора и рафинера.
Рис. 2. Древесные волокна после измельчения: а) в измельчителе; б) в рафинер
Древесноволокнистый мат формируют на воздухе сухим способом производства или в водной среде мокрым способом производства. Взаимодействие древесных волокон, образующихся в мате, между собой происходит в условиях горячего прессования при изготовлении полутвердой твердой древесноволокнистой плиты или при сушке (для мягкой плиты).
При мокром способе производства (рис. 3) готовое тесто помещают в тестовую ванну, где концентрацию волокна перед разливкой устанавливают в пределах 0,9-1,8%. Обезвоживание ковров происходит последовательно путем фильтрации, отсасывания и отжима. Горячее прессование осуществляется на поддонах с использованием сеток для создания условий для отвода воды и пара. Температура прессования плит 200-215 0С, давление 5,0-5,58 МПа в фазе прессования с последующим снижением в фазе сушки и повышением в конечной фазе — твердении.
Рис. 3. Схема технологического процесса твердых и сверхтвердых плит: 1 — щепа; 2 — круглый лес и кусковые отходы; 3 — отбойник; 4 — циклон; 5 – сортировка стружки; 6 — бластер; 7 — емкость для связующего; 8 — емкость для парафина; 9 — емкость для серной кислоты; 10 — пакеты с эмульгатором; 11 — эмульгатор; 12; тринадцать; 14 — расходные емкости соответственно для осадителя, парафиновой эмульсии и связующего; 15 — жетонный бункер; 16 — установка для промывки щепы; 17 — конвейерные ленты; 18 – расходный бункер для рубительной щепы; 19 — дефибратор; 20 — рафинер; 21 — рафинировочный бассейн; 22 — массовый таз; 23 — короб сплошной склейки; 24 — разливочная машина; 25 — пресс, 26; 35 — загрузочно-разгрузочное устройство; 27 — автомобиль
Сверхтвердые плиты получают введением дополнительной операции пропитки прессованных плит маслами, после чего плиты отправляются на термообработку. Термообработку прессованных плит в специальных камерах проводят при температуре 160-170 0С.
Схема получения мягковолокнистых плит мокрым способом производства аналогична схеме получения твердых плит. Однако отсутствуют такие операции, как горячее прессование пластин и окончательная термообработка (рис. 4).
Мокрое производство ДПВ организовано таким образом, чтобы свести к минимуму потребление воды. Объем сбрасываемых сточных вод находится на уровне 3 м3/т плит.
Рис. Рис. 4. Схема технологического процесса изготовления мягкой плиты: 1 — конвейер подачи щепы; 2 — дефибратор; 3 — рафинер; 4 — мельница третьей ступени измельчения; 5 – бассейн промежуточных масс; 6 — расходная чаша для теста; 7 — сплошная проклеивающая коробка; 8 — разливочная машина; 9 — зарядное устройство; 10 — вальцовая сушилка; 11 — устройство форматной резки; 12 — стопка плит со склада готовой продукции.
2. Технология изготовления ДВП по сухому способу производства
Схема для сухого способа производства ДПВ (рис. 5) показывает, что цех подготовки древесины типичен для производства других видов плит. Кондиционированная стружка поступает в паровую камеру, раствор связующего распыляется на волокно на выходе из измельчительной установки. Сушка волокна осуществляется в два этапа. На прессованное волокнистое покрытие наносится финишное покрытие. Пластины прессуются на позиционных прессах при высокой температуре: 220-260 0С. Максимальное давление прессования 6,5-7,5 МПа. Камера кондиционирования выполняет две функции: увлажнение и охлаждение.
Для повышения прочности и водостойкости прессованных плит на фенолформальдегидном связующем плиты ДВП подвергают термообработке и только после этого подают на кондиционирование.
Рис. Рис. 5. Схема производства ДВП сухим способом: 1 — рубительная машина; 2 — циклон; 3 — установка сортировки щепы; 4 — бластер; 5 – бункер для хранения щепы; 6 – расходный бункер для щепы; 7 — паровой аппарат; 8 — расходные баки парафина и вяжущего; 9 — помольная установка; 10 – циклон сушилки первой ступени; 11 – сушилка второй ступени; 12 — формовочная машина; 13 – допечатный ленточный пресс; 14 — головка формовочная отделочного слоя; 15 — поперечная пила; 16 — пила продольной резки; 17 — грузовая полка; 18 — пресс; 19 — скачать что угодно; 20 – камера кондиционирования; 21 — продольный разрез; 22 — поперечное сечение; 23 — пластинчатый аккумулятор; 24 — вилочный погрузчик
3. Технология изготовления MDF
Технологическая схема производства плит МДФ включает три основных этапа: производство древесного волокна, формирование мата и горячее прессование (рис. 6).
Рис. 6. Технологическая схема производства МДФ
Для изготовления плит используют кругляк, кусковые отходы и технологическую щепу как из хвойных, так и лиственных пород, а также другие виды древесноволокнистых плит. Сырье перерабатывается в цехе подготовки древесины, где установлены окорочные машины, рубильные машины, системы транспортировки щепы и коры. Для очистки щепы от посторонних включений кроме операции окорки круглого леса предусмотрена операция промывки щепы.
Основой для производства качественных плит МДФ является также качественное древесное волокно, получаемое, как и при сухом способе производства плит ДВП, методом Дефибратора.
Полученное волокно направляют на сушку, которую проводят в пневматических сушилках с ограниченной температурой охлаждения, не превышающей температуру начала термического разложения компонентов древесного комплекса, которая составляет 180 0С. Основные типы применяемых сушилок — традиционные одноступенчатые и прогрессивные двухступенчатые, в которых процесс сушки протекает более плавно, чем в первой, а также минимизируется риск преждевременного отверждения связующего и пересушивания волокна.
Процесс сушки в трубчатой сушилке осуществляется за счет подачи сырого волокна в потоке горячего воздуха.
По мере прохождения волокна от узла измельчения к сушилке водный раствор вяжущего впрыскивается в массовый поток через форсунки или дисковые распылители.
Качество формирования волокнистого мата определяет однородность характеристик МДФ. Мат формируется с помощью станции механической формовки мата. Тесто из бункера-дозатора поступает на разбрасывающие вальцы и проходит по направляющей пластине на раздаточные вальцы. Для выравнивания ковра по ширине устанавливаются выравнивающие валики, которые выравнивают поверхность ковра и делают его толщину однородной (рис. 7).
Рис. 7. Конструкция формовочной машины при производстве МДФ и внешний вид волокнистого мата на ее выходе (Siempelkamp)
Сформированный ковер проходит предварительную прессовку для уменьшения его толщины и увеличения плотности. При этом из ковра удаляется значительная часть воздуха. Предварительное прессование осуществляется в прессе ленточно-валкового типа без нагрева. Плотность ковра после этой операции около 550 кг/м3
Современные высокопроизводительные предприятия прессуют МДФ на прессах непрерывного действия, которые обеспечивают высокую точность толщины и стабильное качество плиты. Максимальное давление прессования составляет 5 МПа в начале процесса и постепенно снижается до 1,5 МПа. Пресс имеет зону охлаждения на заключительном этапе прессования плит. Это снижает давление парогазовой смеси внутри плиты и исключает образование пузырей и расслоение при выходе плиты из пресса.
После прессования обработка МДФ аналогична той, что используется при производстве ДСП. Шлифовка плит после сквозных прессов производится только для удаления блеска и сглаживания возможных неровностей. Припуск на шлифовку на многоярусных прессах назначают до 1,6 мм.